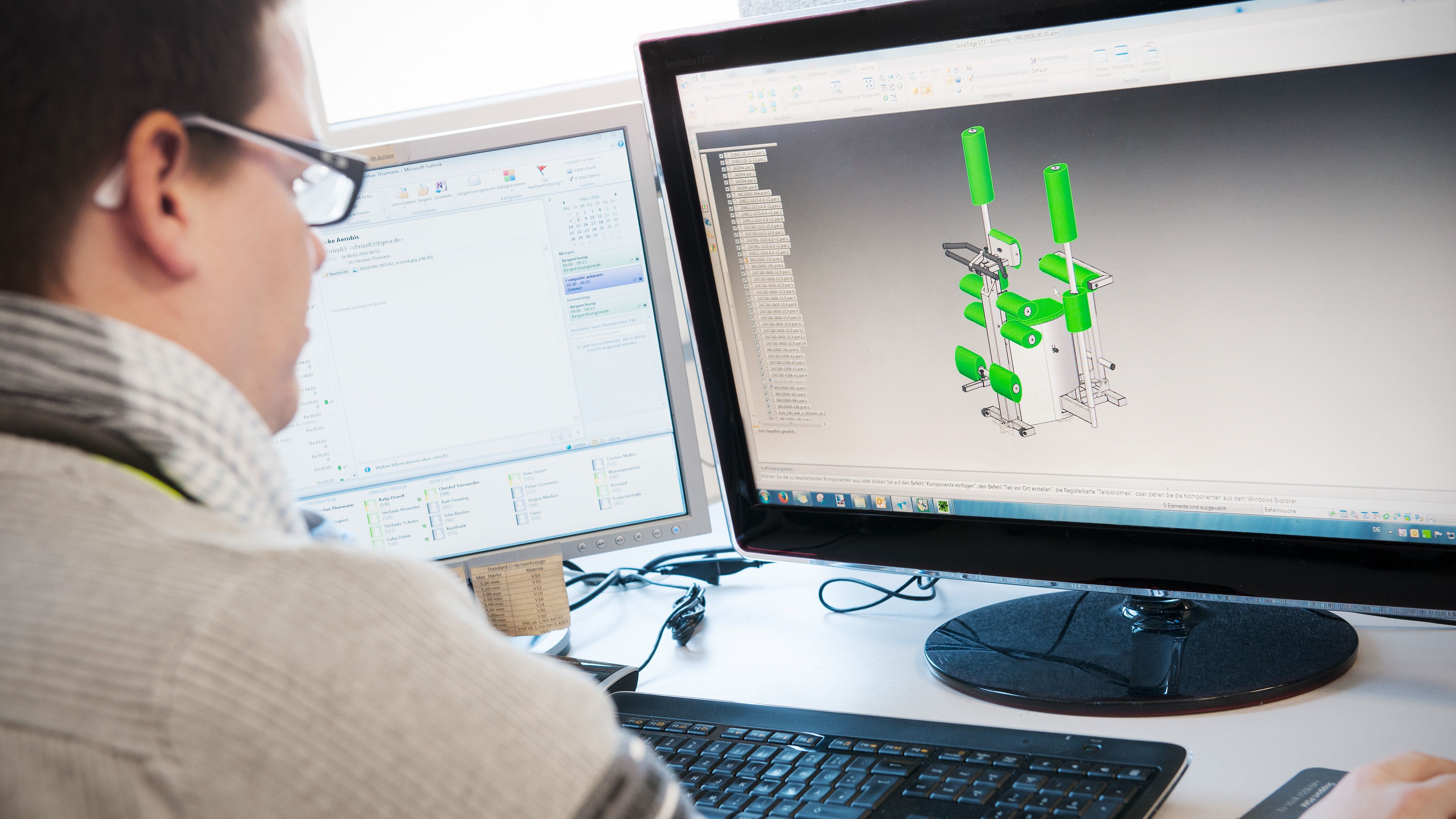
Digitalisierung und Automatisierung bei S&D
Stellenwert der Digitalisierung und Automatisierung ist in der Corona-Krise in den Vordergrund gerückt
Die Pause als Chance genutzt: Die S&D Blechtechnologie GmbH hat die durch reduzierte Auftragslage freigewordene Manpower für Projekte in den Themenbereichen Digitalisierung und Automatisierung genutzt. „Die hier realisierten Projekte bringen uns nachhaltig nach vorne und lassen uns gestärkt aus der Krise hervorgehen“, so S&D-Geschäftsführer Henning Schlöder.
Beschreiben Sie das allgemeine Stimmungsbild in Ihrem Unternehmen.
Die S&D Blechtechnologie GmbH ist ein rheinland-pfälzischer Betrieb in der Blechbearbeitung. Einige Kilometer entfernt von Trier und in unmittelbarer Nähe zu Luxemburg, beliefern wir Kunden mit einfachen Laserteilen bis hin zu komplexen Schweißbaugruppen inklusive Pulverbeschichtung oder komplett montierten Endprodukten. Hierbei liegt der Focus eher auf Bauteilen und Baugruppen mit hoher Fertigungstiefe liegt.
Wir bieten unsere Kapazitäten, unser Fachwissen und effiziente Prozesse an, um unseren Kunden bis zur Warenauslieferung -mit unserem eigenen Fuhrpark- ein treuer und kompetenter Partner in der Blechbearbeitung zu sein. Seit der Firmengründung im Jahre 2002 haben wir unser Leistungsspektrum stetig weiterentwickelt und so sehen wir uns nicht nur als Produktionsdienstleister mit hohem technischen Verständnis, sondern auch als Berater – gerade bei aufwendigen Bauteilen und Fertigungsprozessen. So planen und entwickeln wir gemeinsam mit unseren Kunden und profitieren beidseitig von unserer internen Konstruktionsabteilung.
Welche Probleme/Herausforderungen treten(/traten?) in Ihrem Unternehmen während der Covid-19-Krise auf?
Uns hat das Thema Corona total unvorbereitet getroffen. Mit einer Pandemie hatte das Unternehmen in seiner knapp 20-jährigen Geschichte glücklicherweise bis dato noch keinen Kontakt gehabt. Wir haben uns aber relativ zügig darauf eingestellt, natürlich hat man die Nachrichten extrem intensiv verfolgt, sich informiert und versucht einzuschätzen, was da jetzt auf einen zukommt.
Um den Betrieb und vor allem aber unsere Mitarbeiter zu schützen, haben wir mit dem ersten Lockdown ein Schichtsystem in unserem Unternehmen eingeführt. Aufgeteilt in Früh-und Spätschicht konnten wir so unsere Produktionskapazitäten absichern und gleichzeitig verhindert, dass zu viele Kollegen aufeinandertreffen. Unsere Mitarbeiter haben alle Maßnahmen und Entscheidungen mitgetragen und auch aktiv bei der Erstellung von Maßnahmen und Konzepten mitgewirkt. So konnten wir unser Schichtsystem zeitweise aufheben und flexibel reagieren als die Fallzahlen zwischenzeitlich wieder anstiegen.
Um Verunsicherung gar nicht erst aufkommen zu lassen, hat sich die Geschäftsleitung dazu entschieden, regelmäßig Betriebsrundgänge durch die einzelnen Abteilungen zu machen und über den aktuellen Stand in puncto Schichtarbeit, Auftragslage oder Kurzarbeit zu berichten. Von letzterer blieben wir von April bis August auch nicht verschont, wir haben Sie aber versucht so gering wie möglich ausfallen zu lassen und die freiwerdenden Kapazitäten stattdessen, für aus unserer Sicht, wichtige zukunftsträchtige Projekte genutzt.
Durch zusätzliche Vertriebsaktivitäten und einige Projekte von Stammkunden aus weniger betroffenen Branchen konnten wir die Kurzarbeit glücklicherweise zügig wieder sein lassen und haben in der Zwischenzeit sogar schon wieder neue Kollegen einstellen können.
Sie sprachen eben davon, dass Sie die freien Kapazitäten für zukunftsträchtige Projekte genutzt haben. Was meinen Sie damit?
Nachdem auch bei uns die Auftragslage zu Beginn der Corona-Pandemie eingebrochen war, haben wir, wie viele andere produzierende Betriebe auch, damit begonnen Spukschutzwände etc. zu bauen. Relativ schnell haben wir uns dann aber dazu entschieden die freigewordene „Manpower“, zumindest teilweise, für Projekte einzusetzen, für die sonst immer zu wenig Zeit ist und die uns nachhaltig nach vorne bringen und uns gegebenenfalls gestärkt aus der Krise hervorgehen lassen.
Im Wesentlichen waren das Projekte aus den Bereichen Automatisierung und Digitalisierung, Marketing und Personal. Zwei Projekte möchte ich herausgreifen: So haben wir einen Schweißroboter angeschafft und beim Thema Digitalisierung in ein Onlineportal zur Beschaffung von individuellen Laserteilen investiert.
Das Thema Schweißroboter stand in Anbetracht des wachsenden Fachkräftemangels schon länger auf unserer Agenda. Allerdings waren die bisher am Markt verfügbaren Industrieroboter für unsere Anforderungen und Losgrößen nicht wirklich geeignet. Schon in 2019 sind wir auf kollaborative Roboter (Cobots) für Schweißanwendungen aufmerksam geworden. Ab Ende März haben wir uns dann intensiv mit dem Thema beschäftigt und mit Unterstützung unseres Partners, der Firma Abicor Binzel, konnten wir schließlich eine Cobot-Lösung für das MIG/MAG-Schweißen integrieren und bereits am 15. Juni 2020 die Inbetriebnahme feiern.
Die Einarbeitungsphase ist bereits weitestgehend abgeschlossen und die Kollegen in der Fertigung sind begeistert. Im Übrigen hat keiner der Kollegen darüber nachgedacht, dass dadurch sein Arbeitsplatz „wegautomatisiert“ werden könnte, was anfänglich Bedenken unsererseits auslöste.
Der Cobot läuft in der Zwischenzeit eine komplette Schicht am Tag und erleichtert den Kollegen die Arbeit. Die maschinell festgelegten Parameter des Cobot sorgen für sehr konstante Schweißergebnisse und die Schweißnähte sind nicht nur optisch sehr ansprechend und gleichmäßig, sondern auch qualitativ hochwertig und unabhängig von der Tagesform des Mitarbeiters. Der Aufwand für die Nachbearbeitung konnte so deutlich reduziert werden.
Der Cobot ist wirklich einfach zu programmieren und wird derzeit hauptsächlich für regelmäßig wiederkehrende Bauteil ab Losgrößen von 50 Stück eingesetzt. Derzeit denken wir über einen zweiten automatisierten Kollegen nach, der auch etwas größere Bauteile abdecken kann. Einen weiterer wichtiger Schritt in der Automatisierung und Digitalisierung unseres Unternehmens.
Auch unser zweites „Corona-Projekt“, ein Onlineportal für Laserteile, konnten wir bereits kräftig vorantreiben. Die Implementierung hat begonnen und derzeit sind einige Testkunden unser Portal auf Herz und Niere am prüfen. Mit dem Onlineortal können unsere Kunden den Preis für ihre individuellen Bauteile online und in Echtzeit ermitteln und natürlich auch direkt eine Bestellung erzeugen. Der Bestellprozess bis hin zur Produktion ist voll automatisiert, was natürlich auch kürzere Lieferzeiten ermöglicht.
Bisher beschränkt sich das Onlineportal auf die Arbeitsgänge Lasern und Entgraten. Weitere Arbeitsgänge wie das Kanten sind schon in der Planung.
Mit dem Onlineportal wollen wir dem Trend zur Digitalisierung gerecht werden und unseren Kunden einen Mehrwert bieten. Die Erweiterung in aktuelle Softwarelösungen sehen wir als lohnende Investitionen in die Zufriedenheit unserer Kunden.
Werden wir wieder zu einem „Normalzustand“ wie vor der Krise zurückkehren oder werden sich Prozesse und Abläufe künftig dauerhaft ändern? Wenn ja, mit welchen Änderungen rechnen Sie?
Leider können auch wir nicht in eine Glaskugel schauen und sichere Aussagen über die Zukunft treffen, aber das Thema Corona wird uns sicherlich noch eine Weile beschäftigen und vieles spricht dafür, dass es uns und unsere Umwelt nachhaltig verändern wird. So wird der Stellenwert der Themen Digitalisierung und Automatisierung weiter steigen. In der Krise haben wir uns, wie eben schon beschrieben, verstärkt diesen für uns wichtigen Themen gewidmet.
Aber auch die Meetingkultur hat sich bereits während der Lockdown-Phasen in unserem Unternehmen gewandelt, sodass wir im Kontakt mit unseren Kunden und Lieferanten, aber auch intern des Öfteren auf Videokonferenzen oder -anrufe setzen. Natürlich lässt es sich nicht vermeiden auch Vor-Ort-Termine und den persönlichen Austausch wahrzunehmen, um gewisse Abläufe und Projekte zu besprechen. Aber auch wir haben, wie die meisten anderen Unternehmen, festgestellt, dass es effektiver sein kann den digitalen Weg zu wählen.
Intern hoffen wir, dass ein „Normalzustand“ in Bezug auf Firmenveranstaltungen und Feste, wie z.B. unser Sommerfest, die Weihnachtsfeier oder unsere Laufgruppe, schnell wieder möglich sein wird. Gerade unter den Mitarbeitern merkt man, dass diese Veranstaltungen immer eine tolle Möglichkeit zum Austausch außerhalb des normalen Arbeitsalltages waren.
Gibt es positive Aspekte, die Sie für Ihren Arbeitsalltag aus der Covid-19-Krise mitnehmen?
Wir haben einige Abläufe und Prozesse noch einmal gründlich überdacht und mit Sicherheit auch nachhaltig verbessert. So haben wir bereits in unserer Jahreszielplanung für das Jahr 2021 festgelegt, dass wir das Risikomanagement des Unternehmens noch einmal überarbeiten werden, um Abhängigkeiten zu reduzieren und „Masterpläne“ für gewisse Szenarien in der Schublade haben.
Welchen Herausforderungen abseits von der Covid-19-Krise sehen Sie sich in Ihrem Arbeitsalltag derzeit ausgesetzt?
Auch an uns geht der Fachkräftemangel nicht spurlos vorbei. Wir sind seit jeher davon überzeugt, dass die Ausbildung, so wie wir sie hier in Deutschland haben, eine der Säulen unseres wirtschaftlichen Erfolges ist. Deswegen hat die Ausbildung bei uns einen hohen Stellenwert, der wir zukünftig noch mehr Aufmerksamkeit als sowieso schon widmen möchten. Im Jahr 2020 und 2021 werden die für uns so wichtigen Ausbildungsmessen in der Region Trier fehlen, weshalb wir im neuen Jahr vermehrt auf Social Media aktiv sein werden, um hier unsere Zielgruppe, die potenziellen Azubis zu erreichen.
Hierzu haben wir im Krisenjahr 2020 eine Stelle geschaffen und mit einer neuen Kollegin besetzt, die uns im Bereich Marketing und eben auch beim Thema Social Media unterstützt.
Welche besonderen Projekte haben Sie noch für 2021 geplant?
Es ist nun schon wieder 6 Jahre her, dass wir unser letztes großes Bauprojekt, unsere jetzige „Maschinenhalle“, abgeschlossen haben. Da unsere aktuelle Pulverbeschichtungsanlage ihren 20. Geburtstag hinter sich hat , werden wir auch 2021 wieder ein großes Projekt in Angriff nehmen und eine neue Halle bauen. In dieser findet dann eine neue Pulverbeschichtungsanlage ihren Platz. Die Halle wird eine Größe von 1.800 m² haben. Davon 900 m² für eine neue Pulverbeschichtungsanlage für eine maximale Bauteilgröße von 6.000 x 2.500 x 2.500 mm. Zudem werden in der neuen Halle auf knapp 900 m² Arbeitsplätze für die Herstellung größerer Schweißbauteile aus Stahl entstehen.
Es wird also auch in diesem Jahr nicht langweilig werden.
Quelle: https://www.blechnet.com